The Importance of Recording the Temperature of Every Cell in EV Batteries
Virtually all of today’s electric vehicles use lithium-ion batteries of various chemistries. These batteries require constant monitoring of voltage, current, and temperature to determine the battery’s health and ensure safety. These three measurements are critical during charge and discharge to ensure the battery cells are operating within their safe operating area (SOA). There may also be other sensors in the battery pack being monitored, such as pressure or gas sensors, but typically these function to detect when a cell has already failed. The best practice in lithium-ion battery design is to prevent failures from happening.
While there are voltage measurements on every cell, only one or two current sensors are present per battery pack, and the number of temperature sensors can vary greatly. Large battery packs are typically highly modular, consisting of 12 to 16 cells per module, but with just one or two temperature sensors per module.
Why are there so few temperature sensors, and is it enough?
Few would argue against having more temperature measurements, however, each temperature sensor adds to the total cost of the battery. Typically, temperature sensors are placed at points of interest, such as the side of a 12-16 cell module, or at the end of the pack in modern Cell-to-Pack designs. These are inevitably some distance from the monitoring boards. Building a network of sensors, wiring, and connectors into a pack adds weight, material costs, and design complexity. These economics are a significant limiting factor, and principally dictate the number of temperature sensors in a battery pack.
How do we overcome the economic limitations of additional temperature sensors?
Each Dukosi Cell Monitor includes a built-in, on-die temperature sensor. Once attached to the cell, this ‘free to use’ temperature monitor doesn’t require additional parts, wiring or connectors. The Cell Monitor also supports up to two further external thermistors, which is ideal for larger cells or to reach other important areas. So, instead of one temperature measurement covering four, or eight, or even more cells, Dukosi chip-on-cell technology can perform up to three real-time temperature measurements per cell.
In electric vehicles, the Dukosi chip-on-cell architecture uses a single bus antenna and contactless, near field connectivity and Dukosi’s C-SynQ® communications to simplify the design and enhance long-term reliability. Read more about Dukosi C-SynQ >
Are there other benefits?
Simply: greatly improved safety. Let’s explore how monitoring the temperature of every cell achieves this.
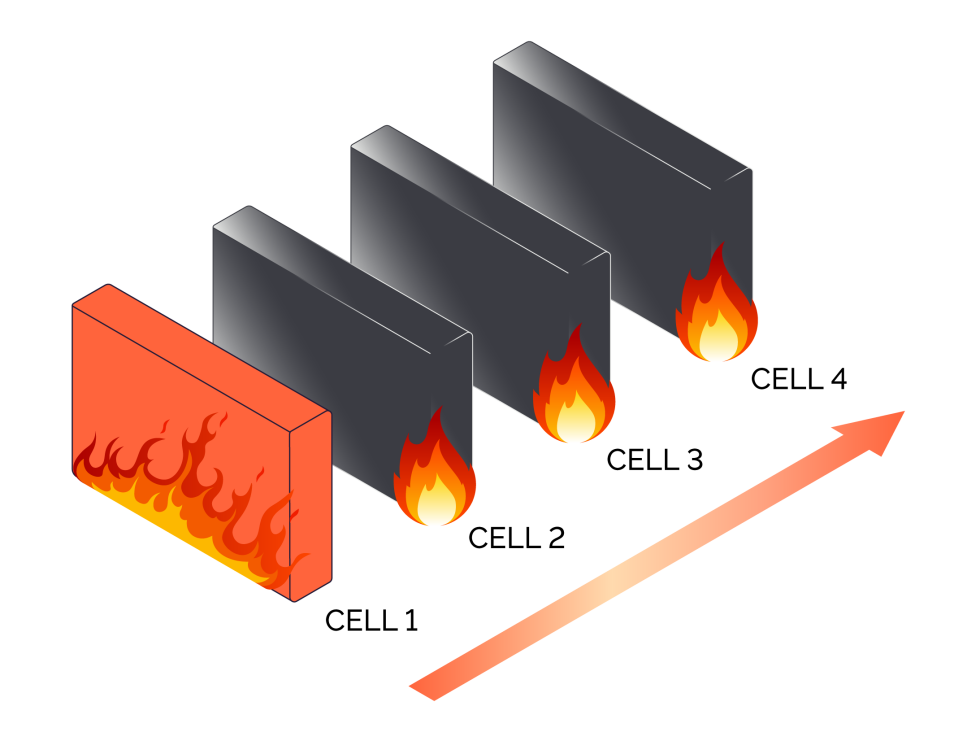
Time to failure determination
Consider a scenario where a number of prismatic cells are configured in a row within a single module. Assume one temperature sensor for every eight cells, which is a typical case. One of the cells is damaged, so its temperature starts to rise, and in this scenario the cell temperature exceeds the manufacturer’s maximum temperature. However, this cell doesn’t have a temperature sensor; in fact the closest sensor is several cells away. Different pack configurations may allow for more efficient distribution of sensors, but in the best possible case, 87.5% of cells will not have a sensor on them and will depend on the rise in temperature in one cell propagating through one or more adjacent cells for it to be detected. If the cell subsequently cools down, the damage may never be detected, but the pack should really be taken out of service.
In a worst-case scenario, the temperature of the damaged cell continues to rise, creating a ‘thermal runaway’ event. Eventually, the cells vent combustible gases and cause the separator between the electrodes to melt. The cell is now on fire, and there is a real danger that fire will propagate to neighbouring cells.

Cell 1 was subjected to a heat source for around 4 minutes (250 seconds) and its temperature rose quickly to about 170°C. The heat source was removed, but thermal runaway had already started. This can be seen in the subsequent exponential rise in temperature occurring in the following 10 minutes. The model then showed a near instantaneous rise in temperature to nearly 380°C, modelling the remaining energy in the cell being released all at once, as the cell ‘burnt out’. Meanwhile, the adjacent cell 2 began rising in temperature during this period, as the heat from cell 1 conducted into it. 10 minutes after cell 1, it too is in thermal runaway, eventually burning out around the 27-minute mark. This cascaded into cell 3 and cell 4 with accelerating impact and temperature, which peaked at nearly 400°C and just over 500°C as cell 3 and 4 burnt out respectively.
If a temperature sensor had been present on cell 1, we would have been alerted to the problem when it reached a threshold value, for example 80°C, which occurred in just over a minute. In this simulation, a temperature sensor on a neighboring cell did not register a similar failure for another 7.5 minutes (5.6 times slower), when two cells away, the delay is over 15 minutes (11.25 times slower), and if three cells away, 25 minutes (18.75 times slower).
This is a simplified example of a typical battery pack, whereas a well-designed pack will feature gas and pressure sensors that would register such a catastrophic failure once the first cell starts venting hot gases, but even that is almost 10 minutes (7.5 times slower) slower than using a temperature sensor located directly on the damaged cell.
Of course, this problem is well understood, and special materials are used to contain the heat and prevent propagation. However, this does not overcome the fact that there may be a delay of minutes before the problem is identified. It is not difficult to see how that delay is a critical safety problem that could be solved by placing a temperature sensor on every cell.
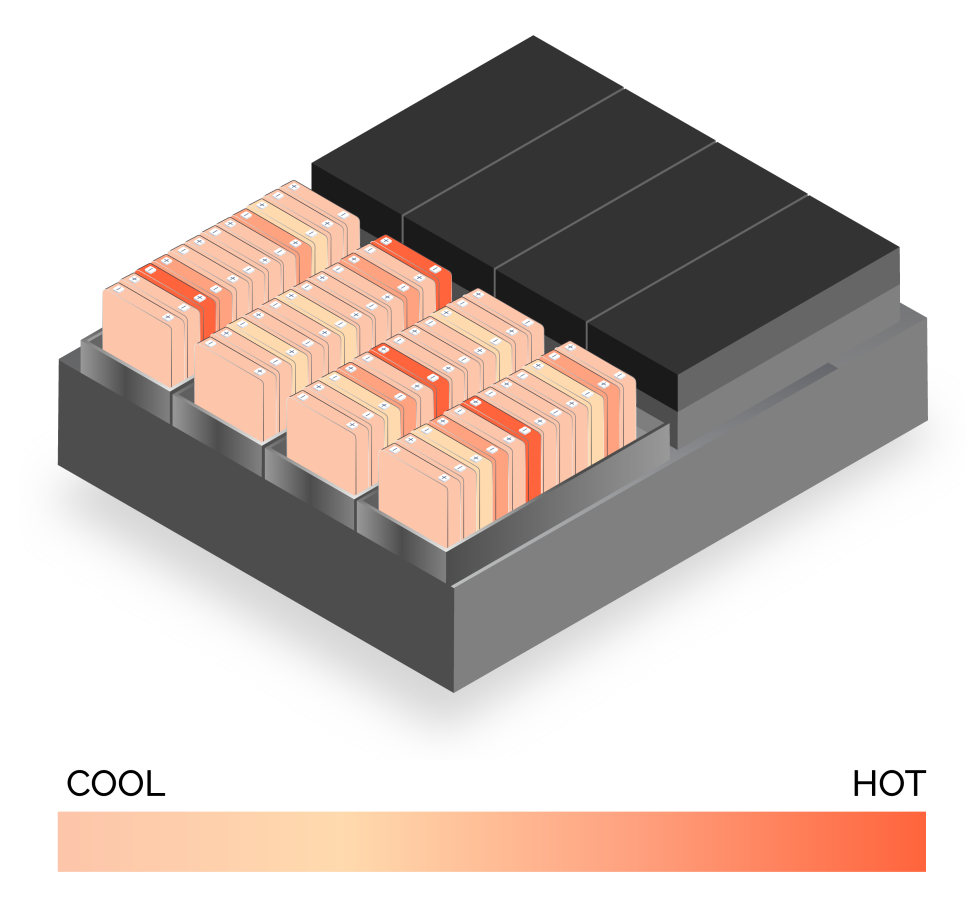
Temperature mapping to immediately spot the problem cell
To maximize safety, we should not wait until a cell is in thermal runaway before we identify a failure. By measuring the temperature on every cell, we can identify when a single cell is warmer than others, even if it’s still within the SOA.
When a battery pack is charged, all the cells heat up. Due to manufacturing variations, there will be differences between their temperatures. In this scenario, one cell is getting much hotter than all the others. If that cell does not have a temperature sensor, then its abnormal temperature rise will probably go unnoticed. With a sensor on every cell, the errant behavior of that one cell can be identified immediately.
Faster charging and greater energy availability
Thermal constraints often limit how fast a cell can be charged, as high currents generate heat. This causes the cell temperature to rise, and its heat must be dissipated through the cell into its surroundings. If the temperature of every cell is not known, then a fast charging controller must act more conservatively.
Counter intuitively, low temperatures are also a great risk for fast charging as it increases risk of lithium plating and dendrite growth. This causes an undesirable active lithium loss, and it can also weaken the cell when it returns to higher temperatures.
Having a temperature sensor at the same location on every cell enables an identical thermal model to be used for all cells in the pack, unlocking more energy for use safely.
For further reading on this topic, please see this article published by Science Direct.
Conclusion
Dukosi chip-on-cell technology greatly improves charging performance, while at the same time improving safety by mitigating the risk of damage or catastrophic failure from overheating battery cells in electric vehicles, and other battery energy storage applications. These are just a few reasons why recording a temperature measurement on every cell is highly beneficial.
To learn more about the safety, performance and cost advantages Dukosi chip-on-cell technology and C-SynQ can bring to large capacity lithium-ion batteries, please see: https://www.dukosi.com/technology-products