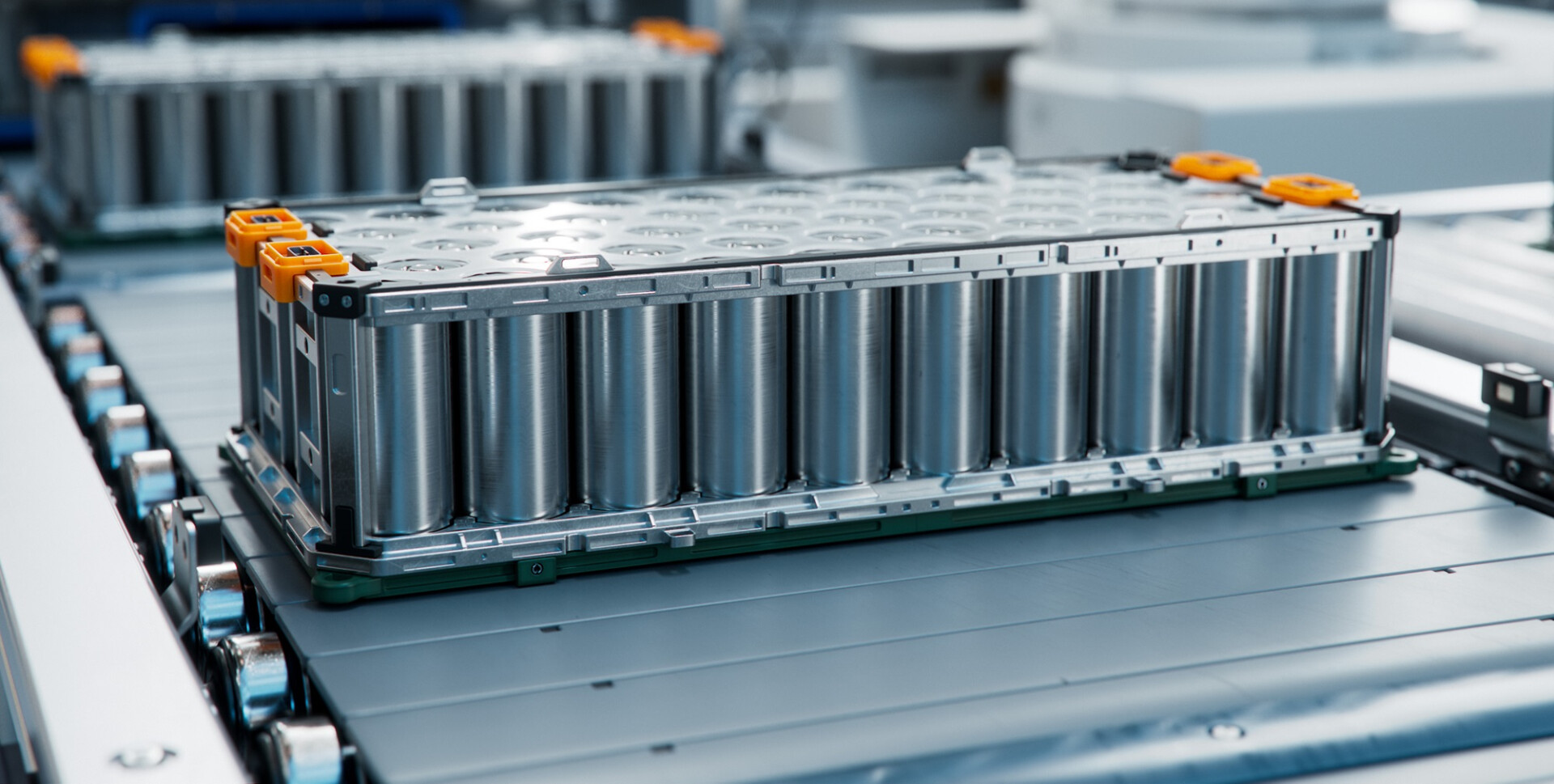
Battery Pack Builders
Leaner, lighter, safer and more flexible battery pack designs
Adapt quickly and meet the needs of next-generation batteries today.
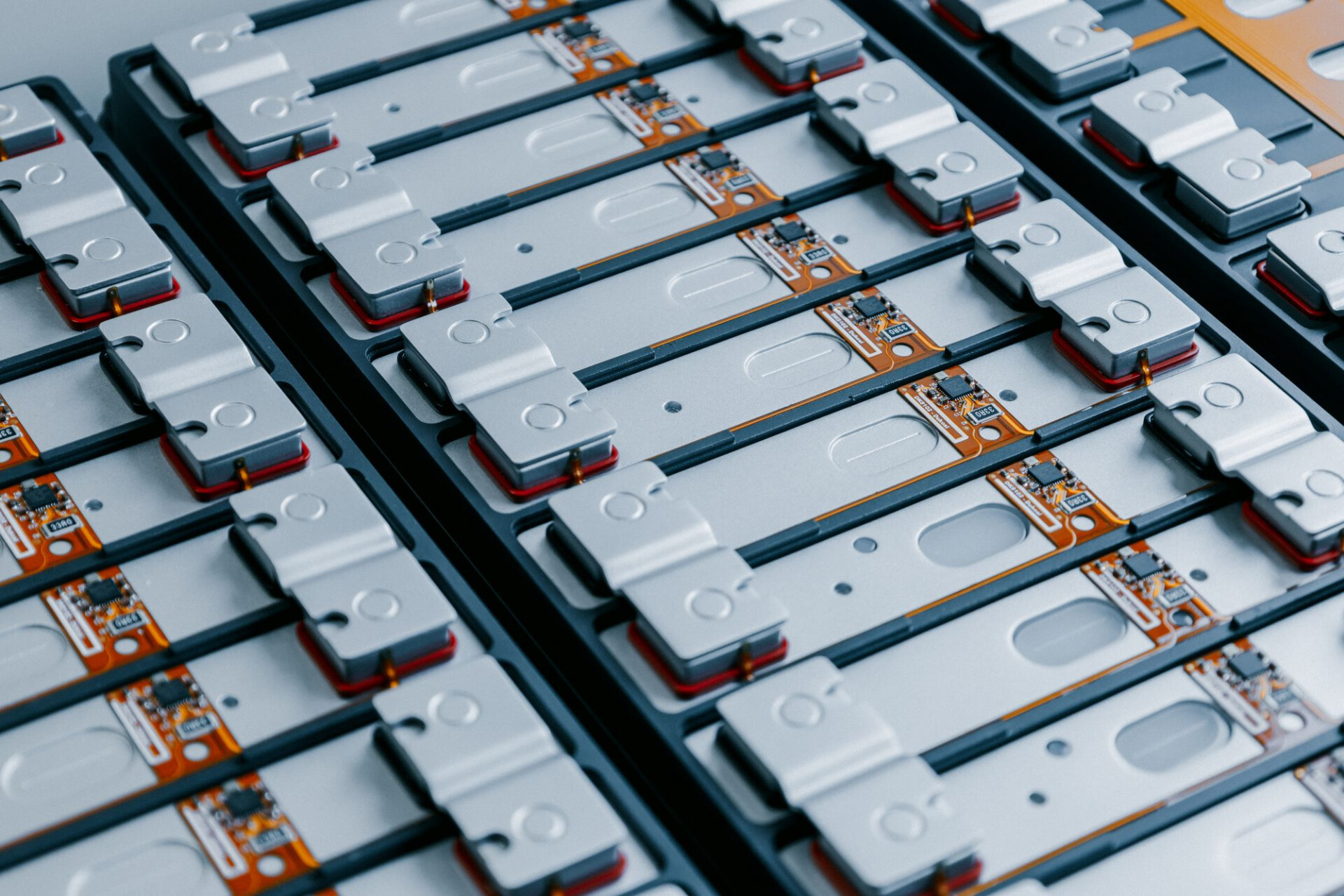
Leaner, lighter, more cost-effective battery pack design
Dukosi Cell Monitoring Solution (DKCMS™) simplifies battery pack designs, allowing them to be physically smaller, lighter, lower BOM, and more efficient to construct by eliminating the wiring harnesses and other associated mechanical components. This allows for more efficient manufacturing processes and greater manufacturing automation.
Improve manufacturing efficiency
The complex wiring harness and associated components usually require time-consuming manual assembly during manufacturing, however by eliminating these DKCMS provides more opportunity for automation, faster production, and reduced operating costs.
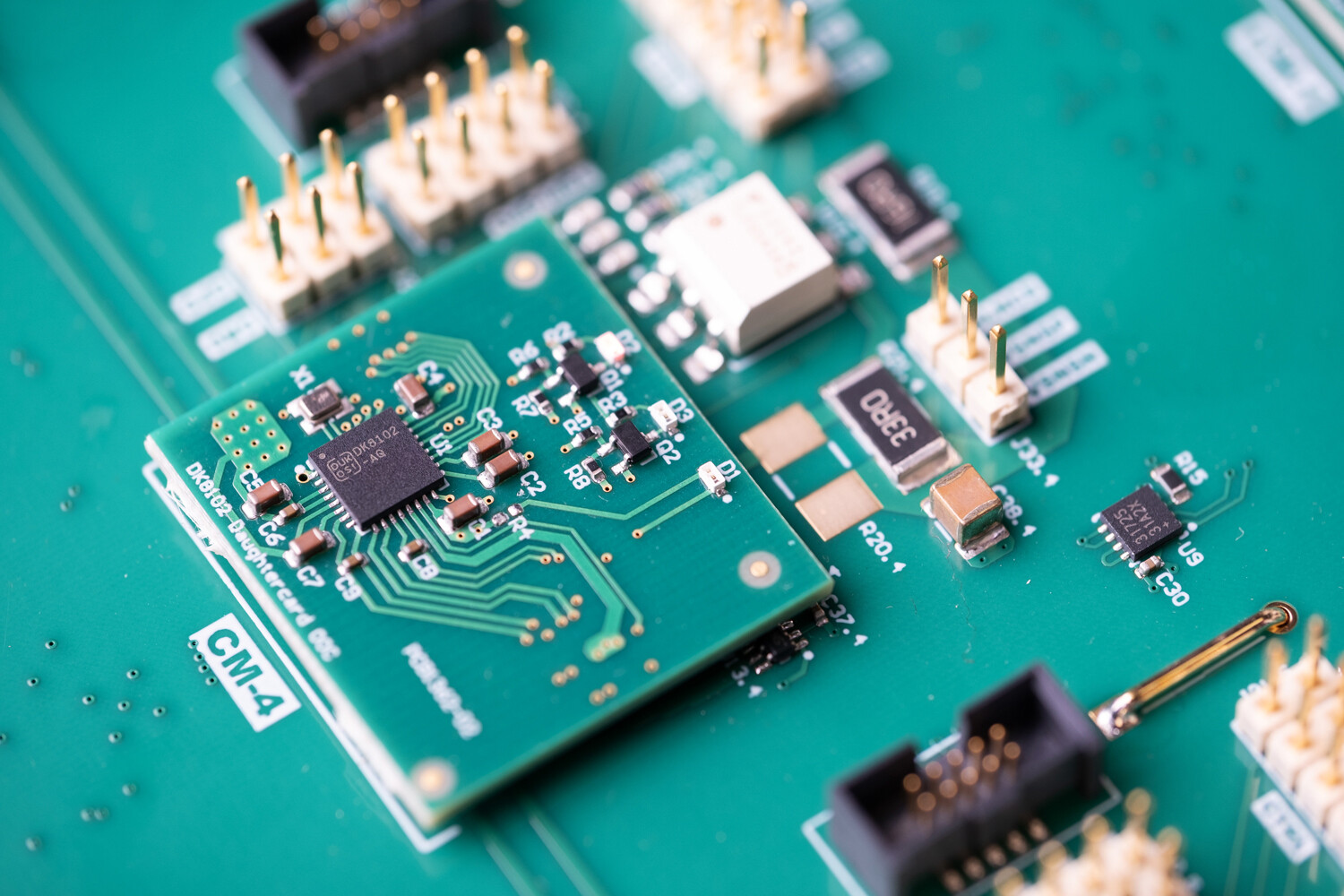
Increase reliability and safety of battery packs
Complex wiring harnesses and associated components are responsible for the majority of reliability failures in batteries. DKCMS eliminates these, replacing it with a patented, contactless communication system based on near-field technology, which improves battery reliability. The architecture is isolated from high voltage areas and also avoids the high voltage sense lead hook up during the assembly process.
Easily assess cell state before production
Battery pack builders can streamline incoming checks and even assess prior shipping and storage conditions by reading each cell’s supply chain information, and an event log that provides an accurate history and state of health.
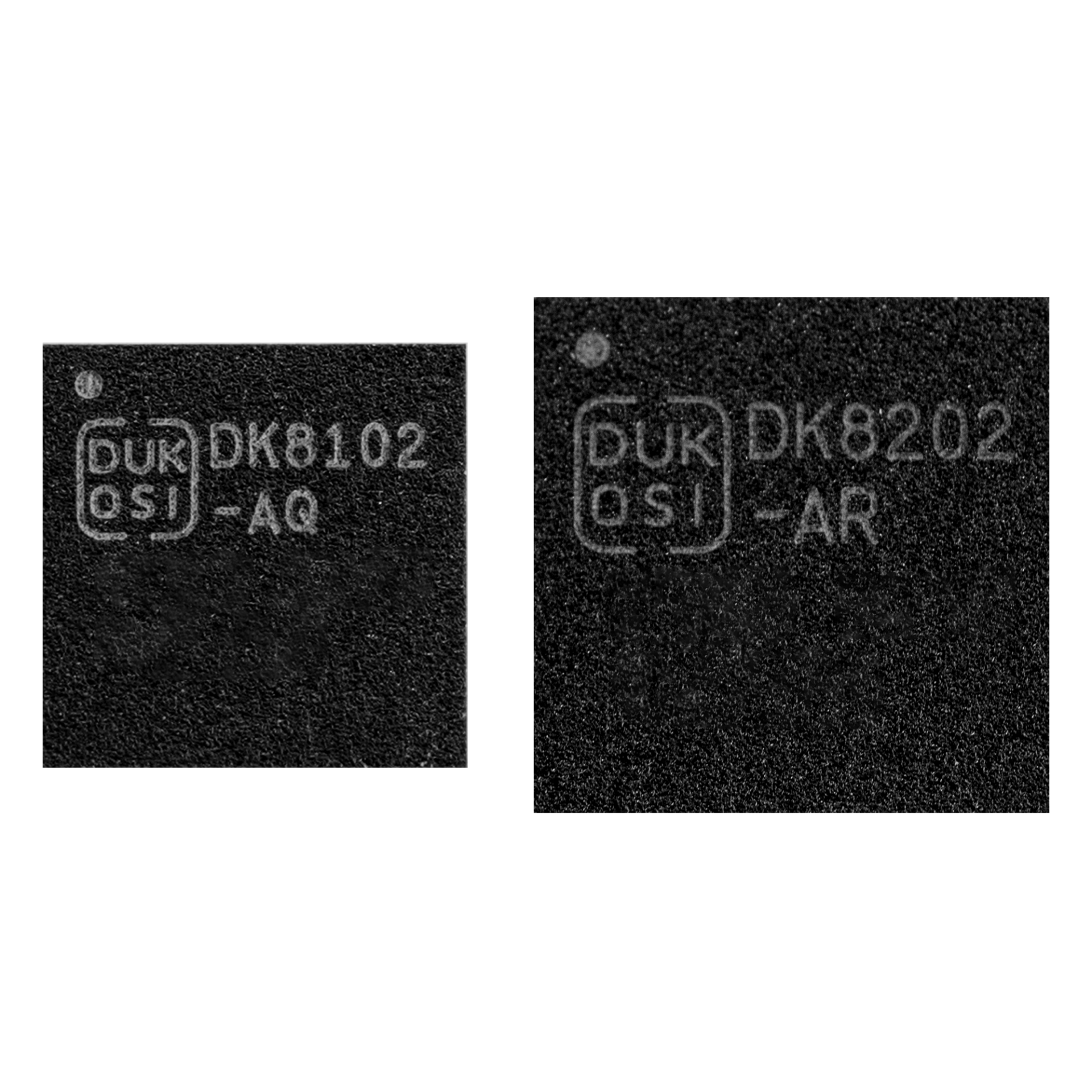
Flexible and scalable architecture
DKCMS’ flexible and scalable architecture enables the latest battery pack designs like cell-to-pack and cell-to-chassis, which improves product differentiation and design options, while also reducing development time, accelerating time to market.
Build big data pools to get ahead of competitors
The collection and analysis of lifetime data from all in use or post-use cells can provide more in-depth usage insights, helping to improve battery pack design and cell management for the current and next generation of batteries in wide-ranging applications.
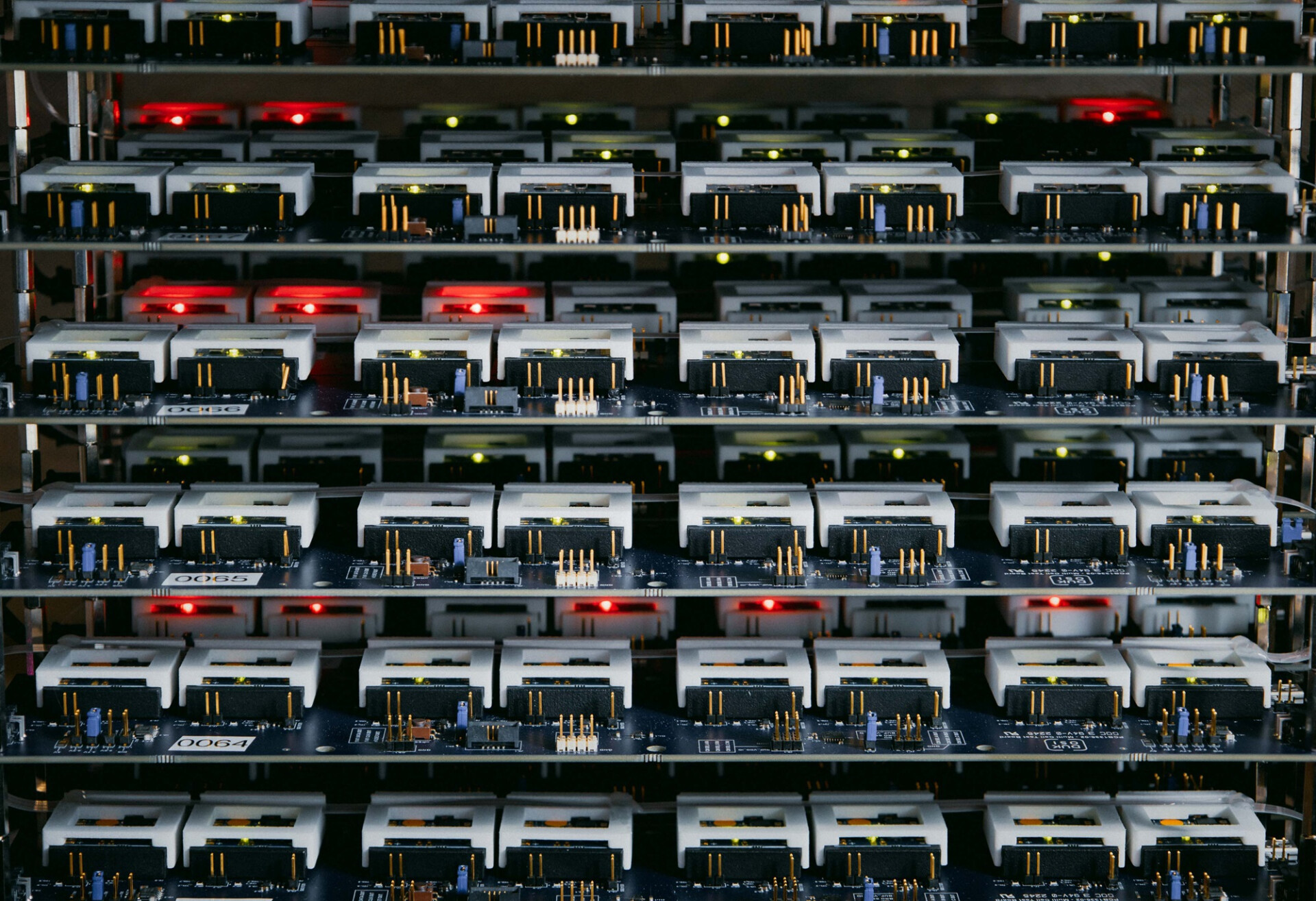
Improve safety in storage and shipping
Battery pack builders have access to data transparency from each Dukosi Cell Monitor, providing more accurate identification and continuous measurement of temperature and voltage, even during inactive times such as storage or shipping.
Reduce liability and warranty costs
Any unexpected cell failure event is logged on that cell1 directly by its Dukosi Cell Monitor. This allows the customer to quickly and easily identify sources of failure, and helps to clearly identify the root cause of warranty claims in the supply chain, avoiding potential conflicts, saving time and costs.
1. In development
Working with Dukosi
At Dukosi, we are driven by our mission to bring revolutionary changes to battery-powered applications. To achieve this, we put active collaboration into practice at technical, operational and strategic levels with our customers and partners. Our partners have been selected based on shared commitment to innovation and excellence, and their ability to deliver strong and trustworthy solutions that help accelerate customers’ development efforts and expedite time to market.