Improving Stationary Energy Storage Performance, Safety, and Reliability
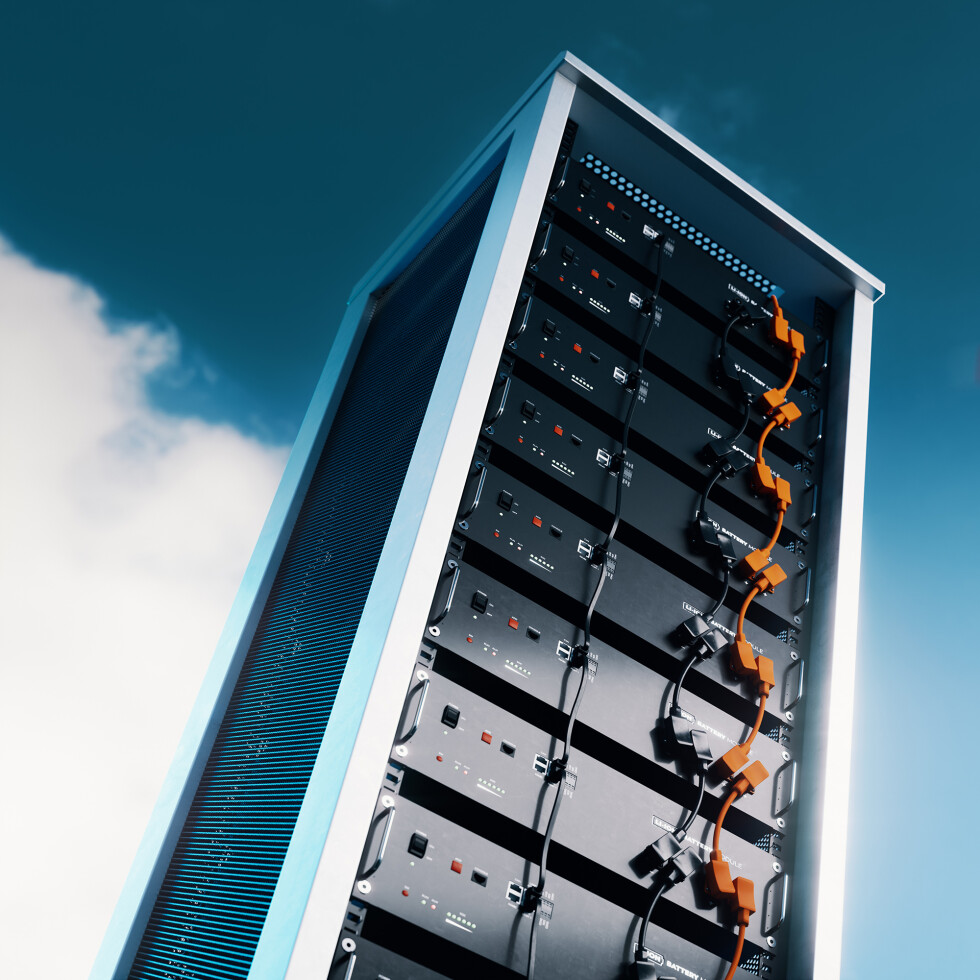
At the core of any stationary energy storage system (ESS) existence is a basic function – store energy at a fixed geographic location and use that energy or power later for its intended purpose. Deeper down within the ESS and after the electrochemical reaction, the pathway to perform the intended service safely, reliably, and more efficiently is the movement of data.
For energy storage in the modern ESS platform, data movement, data interpretation, and data storage to execute specific actions are vital to understand how to charge and discharge a battery, know when to charge and discharge, and identify problems in a battery quickly. Furthermore, communication with the battery and various system components is growing in complexity.
To achieve certain functional safety standards, like those included in UL9540, various system components require closed-loop communication with the battery including a power inverter, charge controller, and other ancillary devices for intermittent renewable generation sources. In addition, adding in auxiliary inputs such as a generator for long-duration load cycles can create further complexities in operation. All these components coming together to work in harmony are made possible by data.
Coming along with the growing complexity of ESS technology is more communication wiring. Manufacturers want to extract as much data as possible for continued optimization of the battery performance – all in the name of more energy density, higher reliability, higher levels of safety, and better warranty support. For example, traditional wiring from a battery management system (BMS) is made to a connection of modules and sub-modules, into packs, aggregating into a main controller with varying sense leads for voltage, temperature, current, and other auxiliary measurements as needed. These connection points can number in the hundreds and thousands per module or pack, creating further points of potential failure. Also, in some module and pack designs, the wiring communication is limited to only monitor and control of data at the module or pack level. Capturing data at the module or pack level only tells a partial story of a battery’s performance. As the old saying goes in the battery industry, your entire battery pack is only as strong as your weakest cell.
Today, with the growing complexities of component networking for operation and ever-increasing connection points for wired systems, an evolved technology is needed to overcome these potential impediments for further market innovation. A technology that can monitor at the individual cell level with very fast speed of data transfer simultaneously over hundreds of cells, while reducing or eliminating intricate wiring schematics of a traditional BMS.
Dukosi’s unique chip-on-cell technology is the first battery management integrated circuit that measures data at each cell and operates wirelessly using near-field communication (NFC) via a single bus antenna. It enables flexible mechanical battery module and pack design, optimizes battery performance, promotes high safety standards, and provides lifetime provenance of individual cell data. In addition, system costs can be significantly reduced: on the battery, during the production process, and throughout the product’s lifecycle.