How is Dukosi Leading the Battery Trends in Electrification?
As the diversity of electrified applications continues to grow, how are battery architectures adapting to meet new demands and challenges?
Traditionally, high-power batteries use wired architectures that rely on aggregated data across groups of cells (modules), but this is proving limiting for a number of reasons. Module level sensing can effectively hinder the speed at which problems at a cell level are detected, undermining reliability and safety, while the aggregated insight provided to the battery management system (BMS) can reduce performance. These factors are the driving motives behind innovative battery designs, such as Cell-to-Pack (CTP) and Cell-to-Chassis (CTC) architectures, that aim to remove the modular layer. If you can shift the monitoring of parameters like temperature and voltage to a cell level, it is possible to increase battery safety, efficiency, and optimize cell loading during discharge and recharge cycles. However, shifting to more granular cell-level monitoring comes with challenges; if using a traditional wired architecture, there would be a significant increase in wiring complexity and connector count. This would be cost prohibitive, more complex to manufacture, and would also introduce more potential failure points, reducing reliability.
A traditional wired battery architecture with multi-channel AFE (left), versus Dukosi DKCMS with a Smart Cell design, near field connectivity using single bus antenna, and proprietary C-SynQ communications (right).
A shift from module- to cell-level monitoring aligns with the market’s trend of improving safety, longevity, and performance, but the additional complexity of design, manufacturing, and maintenance in wired architectures do not support this. Efficient, reliable connectivity is therefore a key enabler for effective cell-level monitoring. A wireless architecture may seem like the most obvious alternative, but electrically noisy, high-voltage batteries presents a number of challenges to achieving it. These are the reasons why we took a different route with our near field contactless architecture for the Dukosi Cell Monitoring System (DKCMS™)1.
A profile representing DKCMS communication: the Dukosi Cell Monitors interact with the bus antenna via contactless near field connection.
What engineering factors were considered, what obstacles were encountered, and how were they addressed in the development of DKCMS?
Designing effective cell monitoring solutions requires balancing accuracy, reliability, and scalability. When we started developing DKCMS, the aim was to enhance performance by capturing real-time, synchronous data on voltage and temperature at the cell level. But equally, it was critical to ensure both the reliability and scalability of the system, ensuring ease of assembly and broad compatibility with diverse battery configurations and chemistries.
DKCMS cell-level monitoring surpasses module-level monitoring by providing real-time, synchronous voltage and temperature data for each cell, allowing the BMS to maximize how the energy in each cell is deployed, while also enhancing safety. However, the significant challenge faced in developing the platform was ensuring that the shift to cell-level sensing didn’t increase the complexity of batteries.
The Dukosi DKCMS Core battery architecture
This challenge spurred the creation of our proprietary contactless communication protocol, C-SynQ®2. Fundamentally, DKCMS is built upon three elements: the cell-mounted DK8102 Cell Monitors, the DK8202 System Hub which facilitates bi-directional communication between the network of Cell Monitors with the BMS host processor, and C-SynQ communication protocol which has been built from the ground up for large networks in safety-critical environments.
Instead of complex wired or a far field wireless connection, DKCMS uses a simple bus antenna routed above each cell monitor to enable the near field contactless communication, providing enhanced security, an increase in reliability of up to 2x, and uses up to 10x fewer components than a typical wired BMS architecture. Furthermore, it is significantly easier to scale battery designs up or down in individual cell increments, rather than whole modules, with the only real design change being the length of the simple bus antenna.
By combining C-SynQ and contactless technology, there is no need to choose between improving flexibility, reliability, or scalability, you can achieve all three; moreover, DKCMS accommodates the latest battery design trends such as CTP and CTC.
What specific safety enhancements does DKCMS provide, and how does this solution compare to other battery architectures?
Fundamentally, contactless technology removes a number of vulnerable wires and connectors which are often a source of failure in high-voltage batteries, but DKCMS also helps engineers to elevate battery safety by capturing real-time temperature and voltage data of each cell instead of at a module level3.
Cell-level voltage and temperature readings of every cell in a pack facilitate more accurate estimations of a battery’s SoC and SoH4, thereby ensuring accurate battery charge(/range) and life estimation. For instance, in a typical module-level design, not every cell temperature is measured. This lack of granular and localized temperature sensing can lead to the delayed detection of thermal anomalies, with potential damage to cells and their neighbors going unnoticed until the heat reaches a thermal sensor, by which time the pack could already be in thermal runaway.
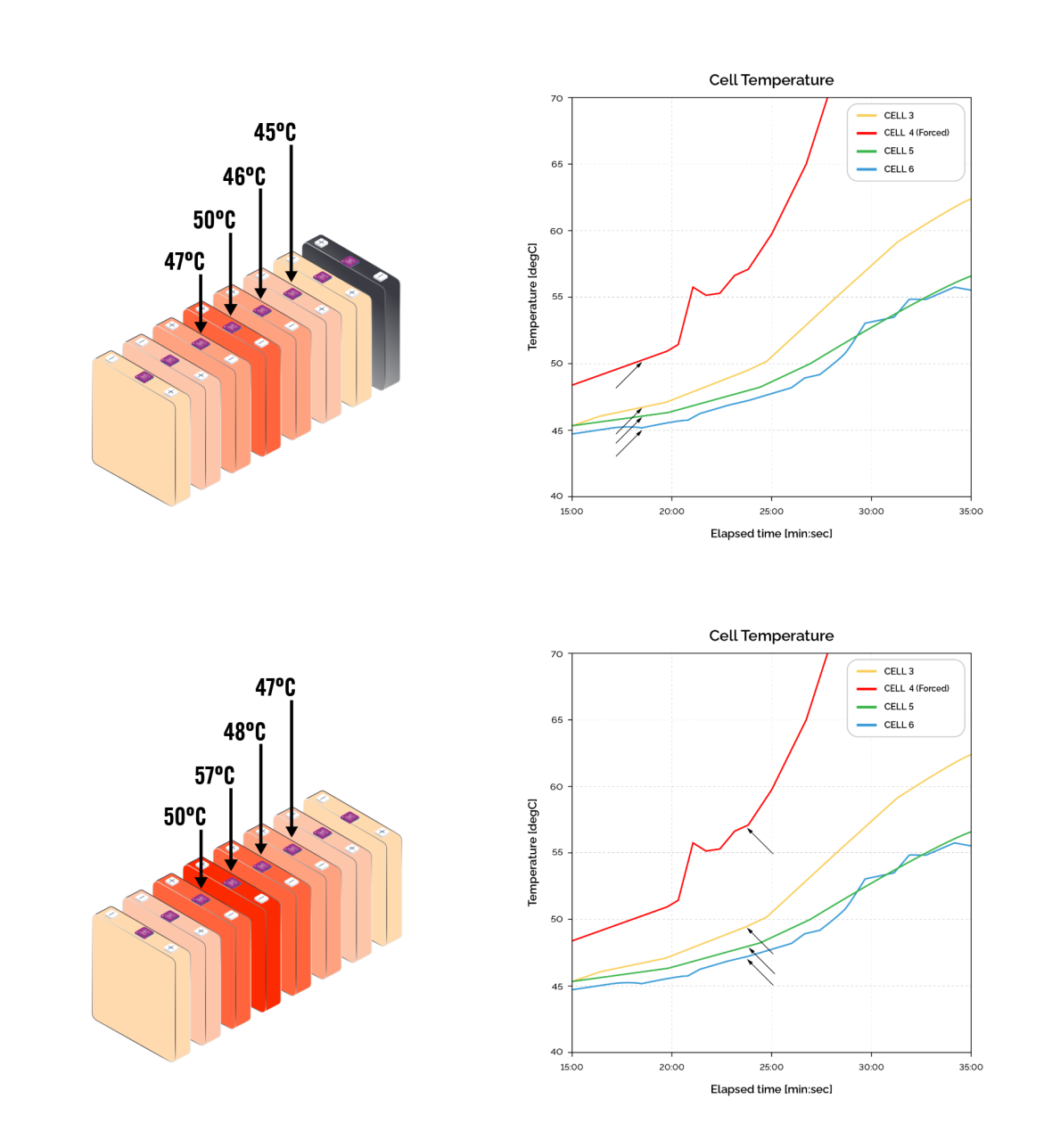
A graphic showing heat propagating between adjacent cells, and the effect of directly monitoring the temperature on each cell.
Dukosi Cell Monitors provides up to three real-time temperature measurements per cell, drastically increasing cell-level insights. This can enhance battery reliability by facilitating earlier thermal event detection and improving the monitoring of safety thresholds during operation. Furthermore, in BESS it can allow for safer maintenance operations thanks to the system’s inherent isolation and the reduction in complex and cumbersome wiring looms.
How does DKCMS support greater manufacturing and supply chain sustainability, especially in the context of battery recycling?
DKCMS’s intrinsic adaptability makes it a key enabler for advancing global electrification and sustainability5. Its ability to seamlessly integrate with various cell types and designs ensures that automotive and industrial batteries can be better optimized for performance and longevity, reducing waste and improving energy efficiency.
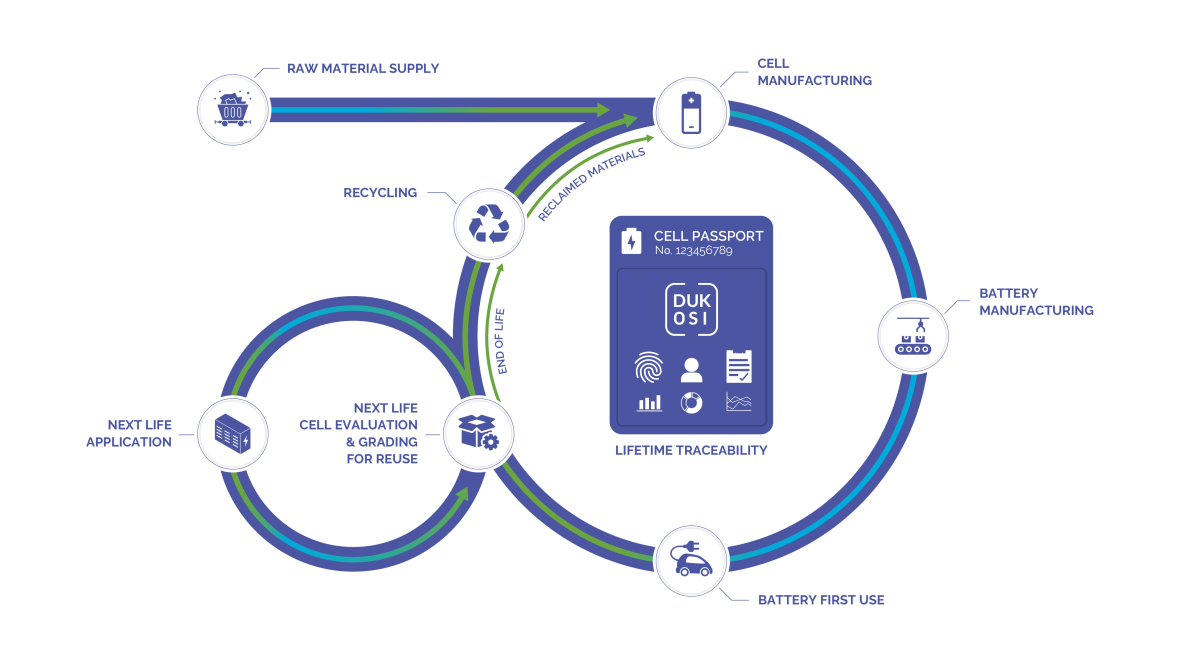
A graphical representation of how Dukosi Cell Monitors support a circular economy and next-life applications for greater sustainability of cells.
In the context of battery repurposing, DKCMS can even facilitate a circular economy by maintaining a digital record throughout each cell’s life, from manufacturing through to end-of-life. This traceability supports initiatives such as the EU battery passport and simplifies the process of evaluating cells for second-life applications, such as energy storage systems, or for material recovery.
By enhancing a battery’s operation to ensure longevity and efficiency, alongside driving more effective battery reuse and recycling processes, DKCMS is designed to minimize the environmental impact of battery production and use of raw materials, contributing to a more sustainable and resource-efficient electric future.
References
- https://www.dukosi.com/dukosi-cell-monitoring-system-dkcms ↩︎
- https://www.dukosi.com/blog/battery-cell-monitoring-with-dukosi-c-synq-is-synchronous-and-deterministic-by-design ↩︎
- https://www.dukosi.com/blog/monitoring-the-temperature-of-every-cell-to-maximize-safety-and-performance-of-high-power-batteries ↩︎
- https://www.dukosi.com/blog/sensitivity-of-lithium-ion-battery-soc-and-soh-estimates-to-sensor-measurement-error-and-latency ↩︎
- https://www.dukosi.com/blog/prioritizing-scalable-sustainable-strategies-to-achieve-net-zero-emissions-2050 ↩︎